高速先生成員--王輝東 關于PCB的背鉆,上期我們講了背鉆XY方向的精準控制《別讓孔偏毀了信號!PCB 背鉆的 XY 精準度如何做到分毫不差?》,這一期我們重點講一下背鉆Z方向(深度)的控制。 PCB 背鉆(Back Drilling)的核心目的是去除多層板中導通孔(Via)在深層多余的 “stub”(未連接的孔壁鍍層殘留),以減少高頻信號傳輸中的反射、損耗和串擾。背鉆深度的精準控制直接影響其效果 ——過深可能擊穿目標層電路,過淺則殘留 stub 導致信號惡化,因此需從設計、設備、工藝、校準等多維度協同控制。 一、設計階段:明確深度基準與理論參數 背鉆深度的理論值需基于 PCB 結構精準定義,為生產提供清晰依據: 1. 明確背鉆的 “終止層” 與 “起始層” o 背鉆深度 = (PCB 總厚度 - 終止層到板底的厚度)± 工藝補償值 例如:某 PCB 總厚 1.6mm,需去除從表層(L1)到 L5 的孔中,L5 以下的 stub(即保留 L1-L5 的導通,去除 L5 到底層 L10 的部分),則背鉆深度應為 “L1 到 L5 的厚度 + 0.05mm 補償”(避免損傷 L5)。 設計文件中需標注背鉆的 “目標深度” 和 “允許誤差”(通常要求 ±0.05mm,高頻板需 ±0.025mm)。 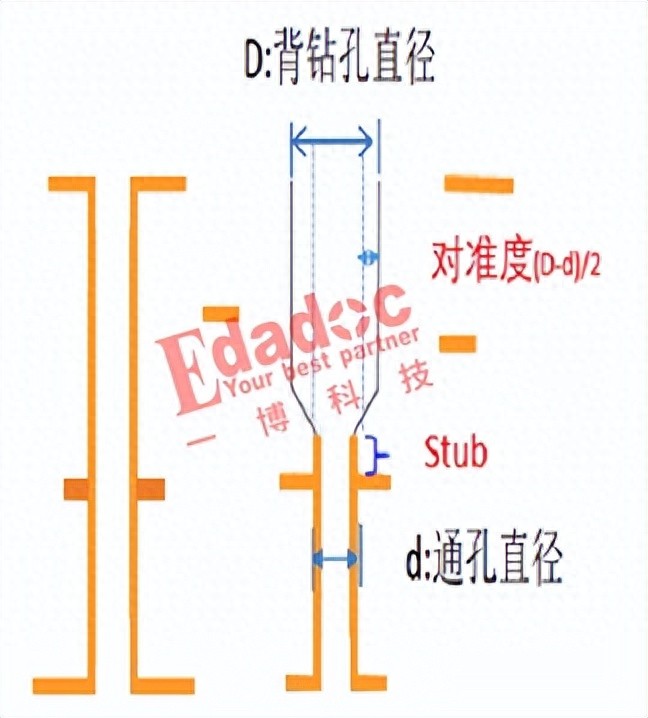
工程輸出時一定要最后輸出背鉆鉆帶,防止因修改資料,導致背鉆通過層,有網絡連接,導致開路。如下圖所示,L1-11層有背鉆通過,L1層有信號連接。 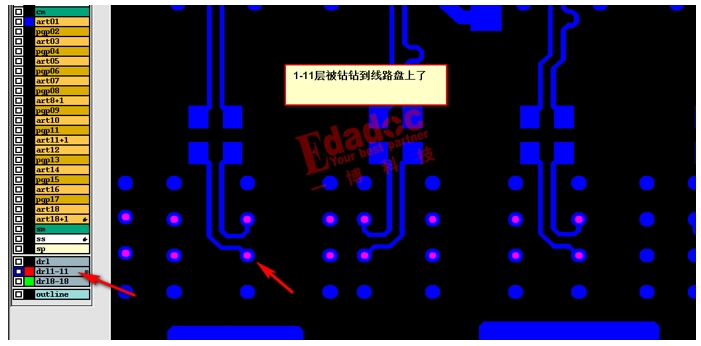
魚眼的深度在哪里 特別是背鉆器件,在設計時一定要精準標注魚眼深度,防止PCB工廠在實際控制時,過分控制stub長度,導致壓接器件開路。 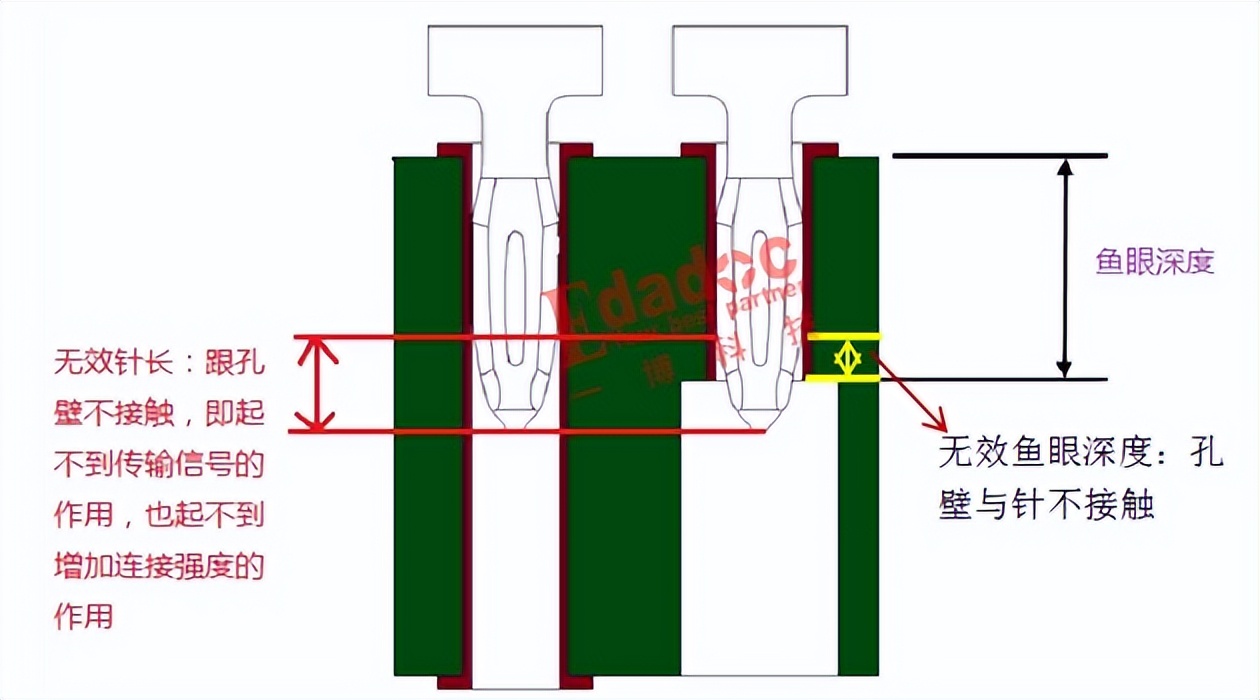
切記,優先控制stub長度,再控制目標層,這個順序一定不要弄反了。 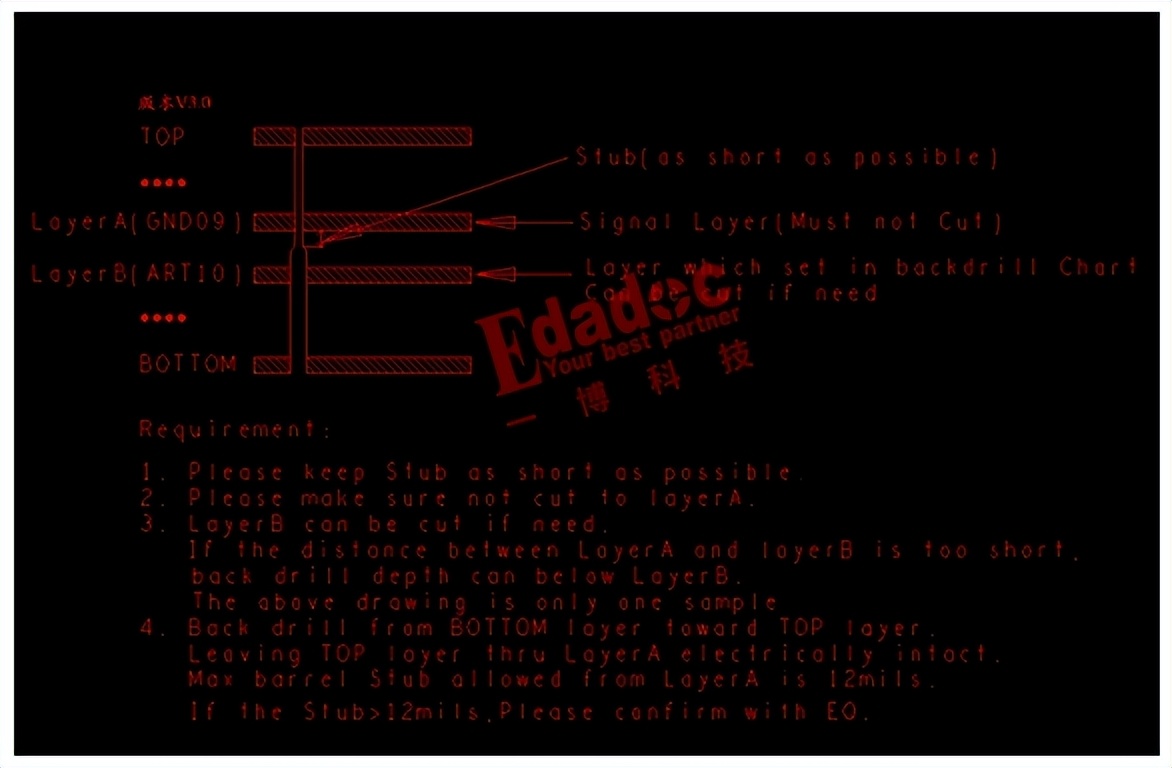
2. 規避設計沖突 背鉆位置需避開內層密集線路或銅皮,預留≥0.1mm 的安全距離(層間介質),防止深度偏差時擊穿內層或者要采用特殊背鉆控制,比如說蝕刻背鉆,增加工藝難度。 同一區域的背鉆深度不宜差異過大,減少鉆機頻繁調整參數的誤差。盡量避免背鉆種類過多。比如同一個區域,有DRL1-3和DRL1-5的背鉆,通過優化設計增加裕量,能否全部按drl1-5去管控stub. 二、設備選型:高精度鉆機是基礎 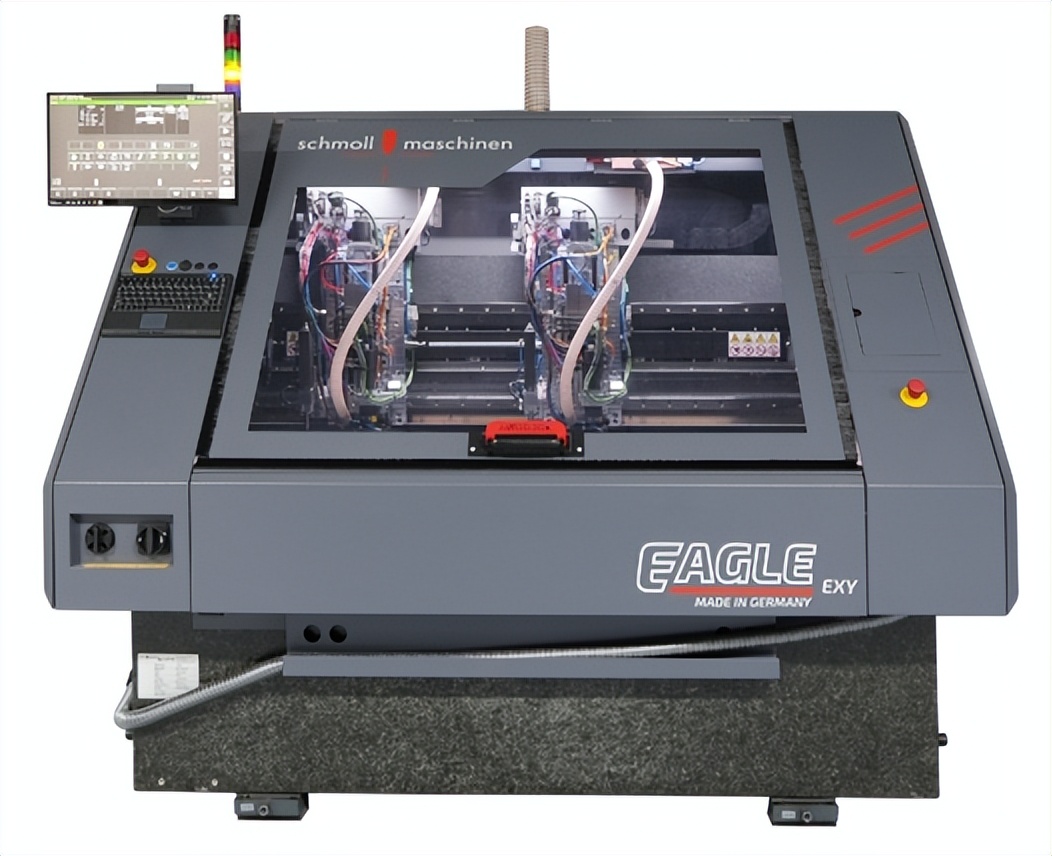
背鉆對設備的 Z 軸定位精度、轉速穩定性和深度反饋能力要求遠高于普通鉆孔,需滿足以下要求: 1. Z 軸定位精度:≤±0.01mm,確保鉆尖下降深度的線性誤差極小。 2. 閉環深度控制系統:配備光柵尺或激光位移傳感器,實時監測鉆尖位置,動態修正深度。 3. 主軸穩定性:主軸徑向跳動≤0.002mm,避免鉆尖偏移導致深度測量不準(尤其針對≤0.5mm 的小孔背鉆)。 4. 光學對位功能:通過 CCD 識別板邊定位孔或 Mark 點,補償 PCB 板的漲縮(熱脹冷縮或加工變形),確保背鉆位置與理論坐標一致(位置偏差會間接影響深度控制精度)。 5. CBD(contact bit detection)控制 深度精度 ±15 微米 無需關鍵調整 長期穩定性良好 因內置專業電子控制,速度快 
三、工藝參數:匹配材料與鉆頭特性 參數設置需平衡 “鉆透 stub” 與 “不損傷內層”,核心參數包括: 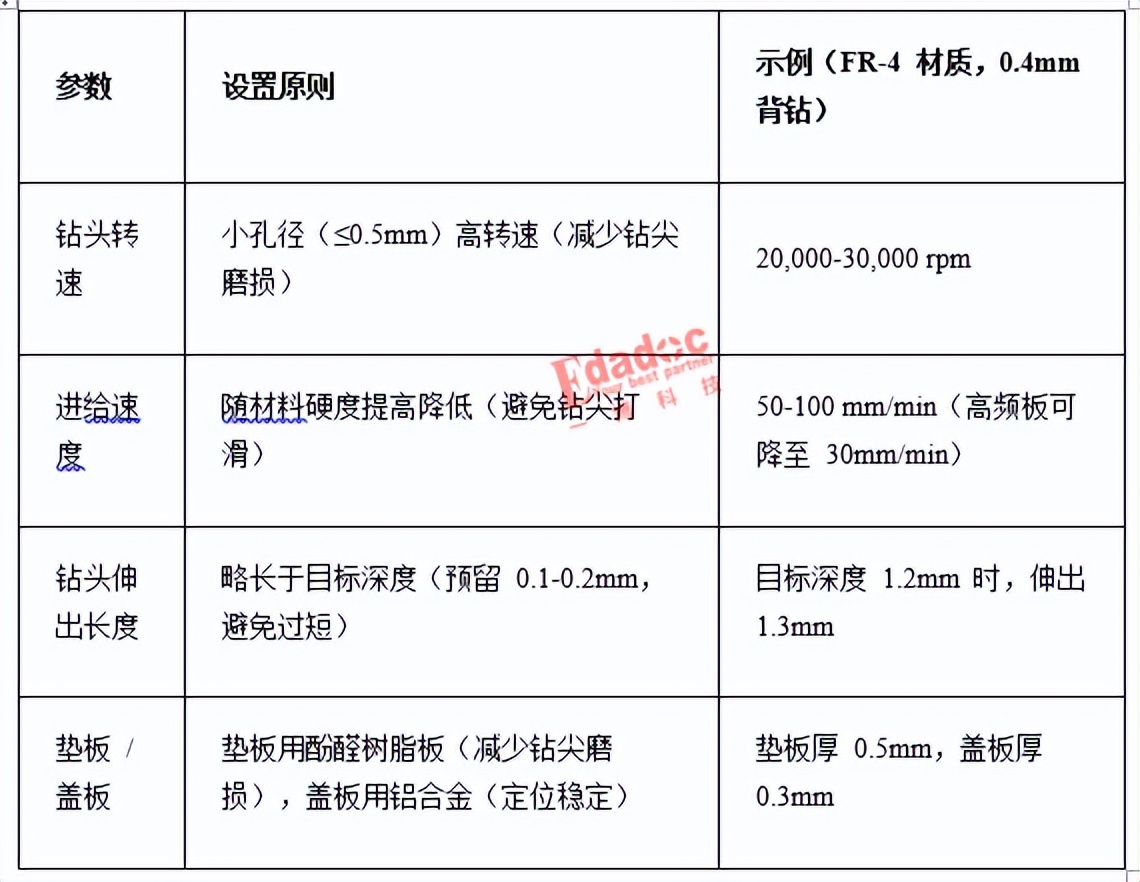
四、校準與補償:消除系統性誤差 1. 鉆頭長度校準 新鉆頭或更換鉆頭后,用 “鉆頭長度測量儀”(精度 ±0.001mm)測量實際長度,與理論值對比,錄入系統補償(例如:理論長度 50mm,實測 49.98mm,補償 - 0.02mm)。 o 每鉆 500-1000 孔后復檢(尤其微小孔徑鉆頭,磨損更快)。 2. PCB 板厚預測量 將一個PCB無限放大以后,PCB的平整度是有偏差,不同區域的厚度有差異,同一批次 PCB 可能因壓合誤差存在 ±0.05mm 的厚度波動,需用千分尺在背鉆區域附近多點(≥3 點)測量實際板厚,取平均值修正背鉆深度(例如:設計板厚 1.6mm,實測 1.62mm,深度增加 0.02mm),現在還有專門的板厚測量儀。 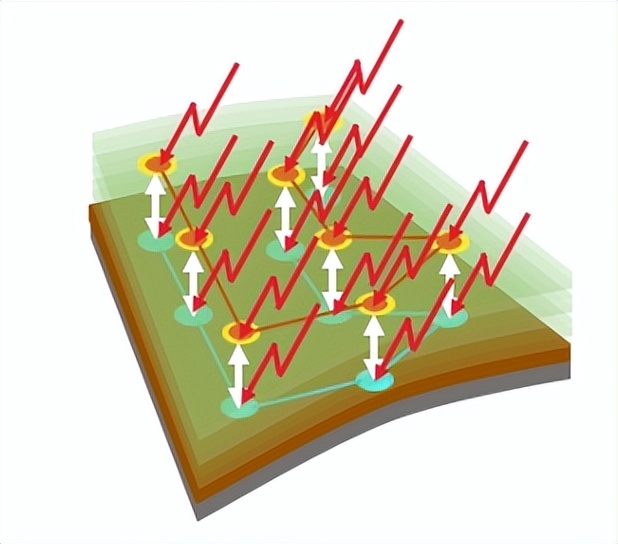
3. 鉆尖磨損補償 鉆尖磨損會導致 “有效切削深度” 減少(如磨損 0.03mm,實際深度偏淺 0.03mm),可通過 “計數補償”(每鉆 N 孔,自動增加 0.01mm 深度)或 “圖像識別”(攝像頭檢測鉆尖磨損量,動態補償)。 4. 專業的背鉆鋁片應用 專業定制化的背鉆鋁片(蓋板),可以提升孔位精度,和深度控制,高散熱,改善孔壁質量 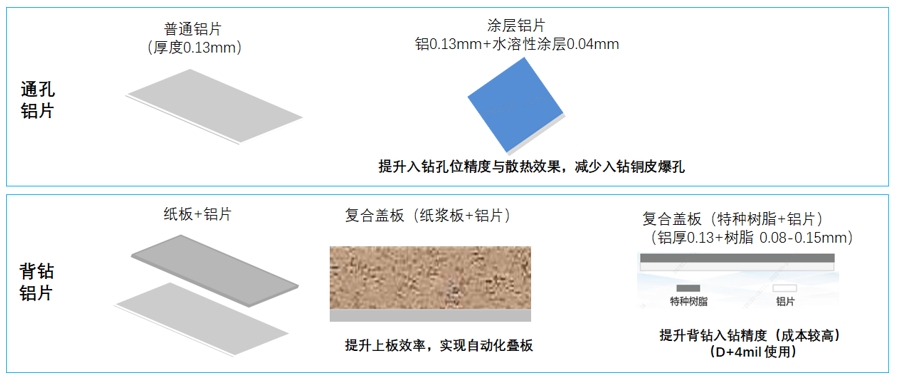
五、過程監控與檢測:驗證深度精度 1. 實時監控 采用 “接觸式深度傳感”:鉆尖接觸 PCB 表面時,傳感器觸發 “深度起點”,全程記錄鉆尖下降距離,超過目標深度 ±0.03mm 時自動停機報警。 紅外測溫監控:若鉆孔區域溫度驟升(超過 150℃),可能因鉆尖堵塞導致進給不暢,間接引發深度偏差,需及時清理鉆屑或更換鉆頭。 2. 離線檢測(首件與抽檢) 切片分析:對首件 PCB 的背鉆位置做金相切片,用顯微鏡測量 stub 殘留長度(要求≤0.05mm)和背鉆底部到內層的距離(需≥0.03mm,避免擊穿)。 X-Ray 檢測:通過 X-Ray 透視背鉆區域,觀察孔底是否與目標內層對齊,計算深度偏差(適合批量抽檢,效率高于切片)。 阻抗測試:對高頻信號孔,通過阻抗儀測量背鉆后的阻抗值(如目標 50Ω,偏差需≤±5Ω),間接驗證 stub 殘留是否達標(殘留過長會導致阻抗偏移)。 六、特殊場景處理 厚板背鉆(≥3mm):采用 “分步背鉆”,先鉆淺深度(如目標深度 2mm,分兩次各鉆 1mm),減少單次鉆孔的應力變形。 多層異質材料:如 PCB 含陶瓷或金屬芯層,需針對不同材料分段設置參數(例如:鉆過陶瓷層時降低進給速度 50%),避免因切削阻力突變導致深度跳變。 總結 精準控制 PCB 背鉆深度需通過 “設計定義基準→設備保證精度→參數匹配材料→校準消除誤差→檢測驗證結果” 的全流程管控,核心是減少 “設備誤差、材料波動、鉆頭磨損” 三大變量的影響。對于高頻、高速 PCB(如 5G 基站板、服務器主板),背鉆深度偏差需控制在 ±0.025mm 以內,需結合更高精度的設備(如進口高精度鉆機)和更嚴格的檢測手段。 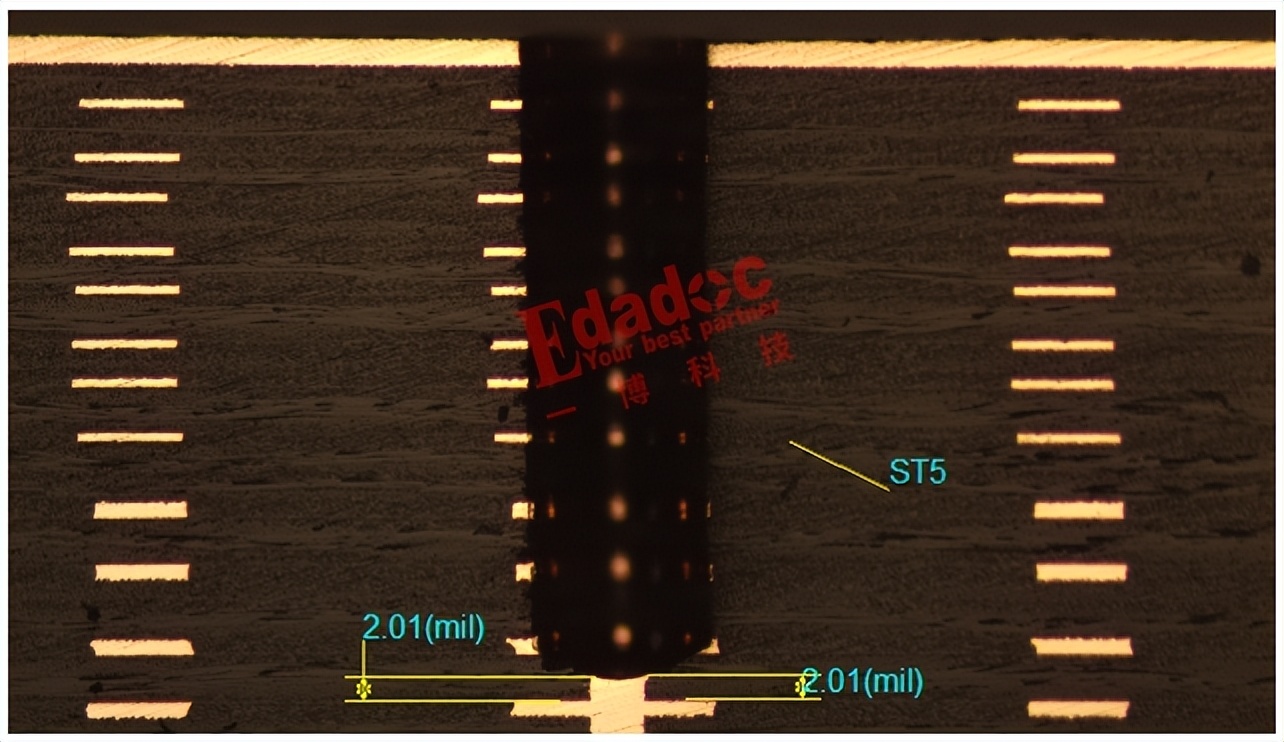
一博珠海全新的PCB工廠,采用德國進口設備,背鉆的STUB可以精準的控制在1-5mil,滿足高速PCB對stub的嚴格需求,歡迎砸單。 本期提問 關于背鉆的加工的stub控制,工廠是否有做出過案例和品質異常,大家一起來聊聊。
|